Recomputing the Bend Solution
Bend calculates a solution using a set of default settings and parameters. Re-calculation of this solution using different settings can be generated. Sometimes, this is also useful to complete the computation after you have interactively edited some tooling or the sequence. For example:
- Change the sequence and ask Bend to compute new tooling stations while keeping the sequence unchanged.
- Change the tooling stations, and ask Bend to compute a new sequence, or to align the part to the newly created stations.
- Try the tooling operation with a different set of tools or try using an already-created setup.
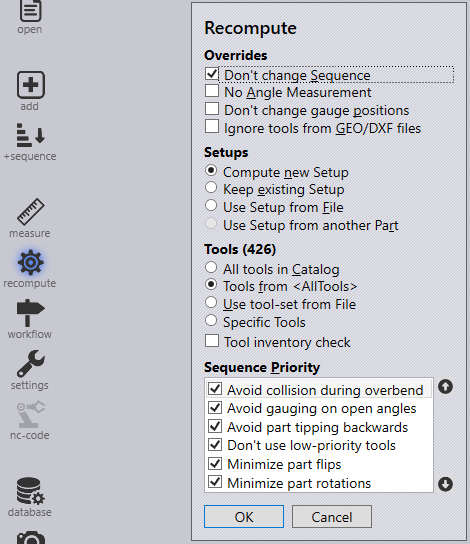
Overrides
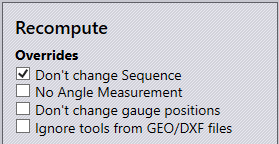
This section contains some switches which can be used to override the default behaviour of the software.
Don’t change sequence – This will compute a new solution without changing the sequence. Different tooling stations, gauging positions or part insertion directions will be tried by the software while holding the sequence unchanged.
No Angle Measurement – Bend computes a solution that performs no angle measurements and will not use any gauging sensors (ACB tools).
Don’t change gauge positions – Original back gauge positions will not be modified.
Ignore tools from GEO/DXF files – This will ignore the tooling hints that can be found in GEO/DXF files.
Setups
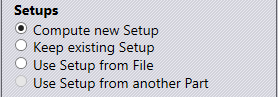
This section sets the strategy for tooling setups. By default, the software will compute the Setup from scratch, these settings change this behaviour.
Compute new Setup – This is the default behaviour. Bend will compute a setup using all the tools it is allowed to (see the Tools section below).
Keep existing Setup – No Setup changes will be made; the software tries to process all the bends using the current setup for the part. If some bends have collisions or have insufficient tool length for processing, those errors remain uncorrected and can be viewed after the recompute process.
Use Setup From File – This option is to use a bend setup file (.bsetup). The Setup loaded from this file is then used for computation; that setup is not modified, nor are any additional stations created.
Use Setup from another Part – This option is available if there are some other parts currently open, and they have been tooled up for the same press brake.
Tools
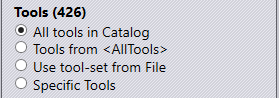
Compute New Setup option must be selected in the Setups section of the Recompute panel for the Tools section to be displayed. Choosing any of the other options in the Setups section, and the Tools section will not be available.
All Tools in Catalog – This is the broadest selection of tools. The software will use every tool available in the manufacturer’s tool catalogue to attempt a solution. While this may mean the solution may not be feasible for production without using the inventory available, it is useful for a speculative exploration of what tools would be required to produce a particularly complex part.
Tools in Inventory – This option will use all the tools that are available in the installation’s inventory. If an inventory of tools is yet to be set up, the software will use all the tools in the Catalogue.
Use tool-set from File – This option is to use a custom tool list (.btools). The Tools loaded from this file are then used for computation.
Specific Tools – This option gives the most direct control over the punches and dies used in the setup as specific tools can be chosen.
Sequence Priority
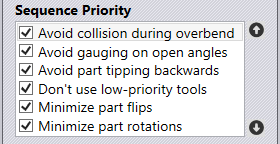
When sequencing the bends in a part, there are a few potentially conflicting requirements. For example, should Bend try to minimize the number of part rotations, or should it try to minimize the bends where the part’s centre of gravity lies inside the machine? Each operator may likely have a different set of priority rules, and also possible that different parts may require different priority settings. Therefore, the sequence priority section allows a re-computation with a different ordering of priorities.
Use the up and down arrow buttons on the right to shuffle the rules; items near the top are higher in priority. Deactivate by unticking the rule; this tells Bend not to consider this as a factor when deciding the sequence.
Avoid collisions during overbend – To achieve angle accuracy, most bends will need to be over-bent slightly to compensate for spring-back. Activating this rule will do bends in such an order that over-bending is possible. For example, in the part below, we should do bend 1 first and bend 2 next; the other order would block over-bending.
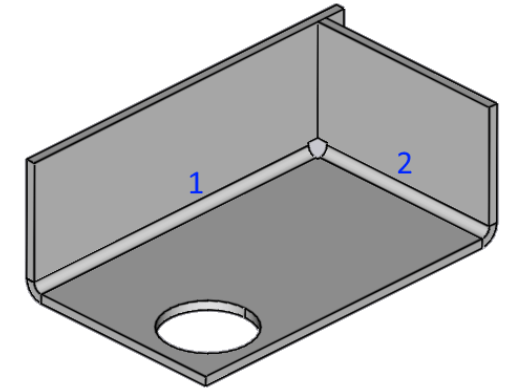
Don’t use low-priority tools – Activate this to avoid using low-priority tools, or tools that are not in the preferred list, as much as possible.
Avoid gauging on open angles – Gauging positions should ideally be in the same plane as the bend axis, and there should not be any already-processed bends between the bend line and the gauging point. Here is an example of poor gauging that this rule tries to avoid:
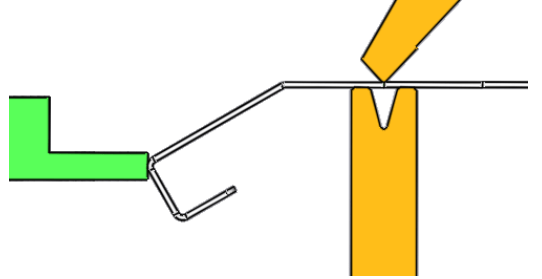
Avoid part tipping backwards – It is useful to avoid situations where the centre of gravity of the part lies behind the tool line. This rule tries to minimize such situations. The software has some discretion about the part weight and how far back the centre of gravity is behind the tool line to consider this as a problem. Technically, it considers a part to tip backwards if there is a tipping moment of 0.15 N-m (Newton-meter).
Minimize part flips – Part flips are when the part has to be overturned (successive bends are in different up/down directions).
Minimize part rotations – A part rotation is when a part is turned left or right in the horizontal plane; this is considered to be easier for the operator than a part flip.